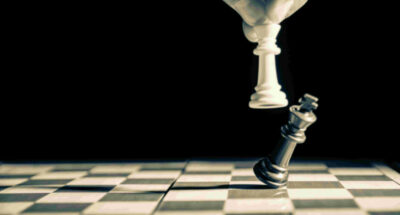
Why leaders should learn to value the boundary spanners
Entrepreneurial talent who work with other teams often run into trouble with their managers. Here are ways to get the most out of your ‘boundary spanners’...
Audio available
by Richard Markoff, Ralf W. Seifert Published November 17, 2021 in Supply chain • 4 min read • Audio available
When supply chain issues first surfaced earlier this year, the initial culprit was a lack of inventory. The argument was that for years supply chain managers had put too much emphasis on working capital, implementing just-in-time inventory management, and relentlessly pushing inventory levels to absurdly low levels. And when hiccups in physical chains emerged, there wasn’t enough safety stock in the chain to absorb the bumps.
This explanation seemed a bit too facile and never passed the smell test. Across all industries, inventory, when compared to demand, is significantly higher than it was 15 years ago. Exploding SKU (stock keeping unit) counts, increased promotions, the demand of e-commerce and shorter product lifecycles have all combined to drive up inventory levels. For upstream manufacturing, all it takes is one component to be missing to stop production completely, and it wouldn’t be possible to have a safety stock on everything.
The discourse has now moved to supply chain infrastructure. Port capacities are not adequate, there aren’t enough containers and there is a shortage of truck drivers.
There is more truth to this argument. Physical supply chains have been hit by labor shortages due to COVID-19 and ships locked in quarantines, causing bottlenecks in moving containers away from ports and on the roads. This is also true for manufacturing, where factories have had difficulty ramping up to full production.
The current supply chain troubles have shone a light on the need to upgrade infrastructure, with the Biden administration very recently announcing significant investment in upgrading ports and dockyards, but it will take time to feel the benefits.
“Physical supply chains have been hit by labor shortages due to COVID-19 and ships locked in quarantines, causing bottlenecks in moving containers away from ports and on the roads”
But a closer look reveals that the real story is one of demand. Demand for goods is higher than it has ever been, and it is exposing the supply chain as hyper-efficient, and we are looking at a process of adaptation.
The pandemic has shifted some spending in the US from services (excluding restaurants and travel) to products. Spending far more time at home, consumers have looked to electronics for entertainment and productivity, home renovation and furniture to improve their surroundings and appliances to improve domestic experiences. This shift was fueled in part by extensive public spending to provide support during the pandemic. The result has been a demand for physical goods that is unprecedented, accompanied by an imbalance of trade with Asia.
On the B2B side, there is some understandable shortage gaming that is going, where companies inflate their true demand out of fear of not having enough. Increased inflation (caused in part by supply shortages and increased freight costs) has increased willingness to hold inventory, further increasing baseline demand.
Physical supply chains were already used to peaks in demand around Christmas. In 2013, the global supply chain had not fully adopted to the new realities of e-commerce and there were high-profile stock shortages at the holidays. Companies like Amazon reacted by adding dedicated shipping capacity under their control, and a new balance was found.
It’s not surprising that supply chains had their capacity stretched, with some misses, at the holidays. If that were not the case, it would mean that supply chains had excess capacity during the rest of the year. That is a sign of supply chains being very efficient, not broken or fragile. What is happening now is as if every day were Christmas for supply chain.
The current supply chains issues are due to a lack of anticipation of profound shifts in demand profiles. These shifts go far beyond what a general manager should expect of his demand planning process. The failure to anticipate them show how demand planning is more than a supply chain process, it is a business planning process, one that is a fundamental strategic role in the enterprise.
Supply chain researcher, consultant, coach and lecturer
Richard Markoff is a supply chain researcher, consultant, coach, and lecturer. He has worked in supply chain for L’Oréal for 22 years, in Canada, the US and France, spanning the entire value chain from manufacturing to customer collaboration. He is also Co-founder and Operating Partner of the venture capital firm Innovobot.
Professor of Operations Management at IMD
Ralf W. Seifert is Professor of Operations Management at IMD and co-author of The Digital Supply Chain Challenge: Breaking Through. He directs IMD’s Strategic Supply Chain Leadership (SSCL) program, which addresses both traditional supply chain strategy and implementation issues as well as digitalization trends and the impact of new technologies.
July 3, 2025 • by Eric Quintane in Audio articles
Entrepreneurial talent who work with other teams often run into trouble with their managers. Here are ways to get the most out of your ‘boundary spanners’...
June 24, 2025 • by Jerry Davis in Audio articles
The tech broligarchs have invested heavily in Donald Trump but are not getting the payback they bargained for. Do big business and the markets still shape US government policy, or is the...
June 19, 2025 • by David Bach, Richard Baldwin, Simon J. Evenett in Audio articles
As governments lock horns in our increasingly multipolar world, long-held assumptions are being upended. Forward-looking executives realize the next phase of globalization necessitates novel approaches....
June 2, 2025 • by George Kohlrieser in Audio articles
Leadership Honesty and courage: building on the cornerstones of trust by George Kohlrieser Published 17 April 2025 in Leadership • 5 min read DownloadSave Trust is the bedrock of effective leadership. It...
Explore first person business intelligence from top minds curated for a global executive audience