However, unlike these clear milestones in manufacturing, Industry 4.0 is a collection of emerging technologies for which a clear definition is elusive â though any technology that can claim to be âcyber-physicalâ or âsmartâ can claim to be an Industry 4.0 technology. Some prominent examples include predictive maintenance, collaborative robots, drones, augmented/virtual reality, 3D printing and digital twins. We have seen definitions of Industry 4.0 so broad that over 400 different technologies can be included under its umbrella.Â
Though the term Industry 4.0 is a bit fuzzy, it also comes with buzz. After all, the word ârevolutionâ is in the name, a word that draws attention. The first Industrial Revolution was a genuine social upheaval, with migrations from a pastoral, agrarian culture to the dense smog clouds of London. Now associated with images of Dickensian poverty and child labor, the first Industrial Revolution also ushered in better health and standards of living.Â
Certainly, at the time many were wondering whether the Industrial Revolution â along with the societal changes it wrought â was a good thing. One of the first industries disrupted by the introduction of steam power was the weaving industry, which provides a vivid example of the trade-offs off the time. While steam power resulted in less expensive textiles, the weavers, replaced by automated looms, protested by smashing their shoes into the gear works, giving us the word âsabotage.âÂ
With this complex history in mind, itâs reasonable, even essential, to ask if the Fourth Industrial Revolution is âTech for Goodâ, understood as providing solutions to societal and environmental problems and improving communities and lives.Â
Societal impactÂ
When contemplating the potential impacts of I4.0, one of the first that likely comes to mind is the consequence of robots replacing humans all through the supply chain. The robots wouldnât just replace workers in factories, but also in all of the distribution centers â of which there are more than ever â that warehouse these products. I4.0 promises a world where robots make the products, move them around, prepare orders, and drive the trucks to deliver them.Â
McKinsey predicts that I4.0 will bring productivity increases of up to 30% in manufacturing. If these predictions of productivity do indeed come to pass, proponents would argue that this would lead to less expensive manufactured goods which, through market mechanisms, would be enjoyed by more people lower on the income ladder. The argument is simply that we will have more, cheaper products to enjoy, and that is a good thing.Â
However, it is difficult to imagine that a compensatory amount of employment would be generated in designing and building the future robots. Nor is it certain that many displaced workers could upskill sufficiently to take those jobs. This leads many to fear a near future of mass unemployment during a long adjustment that may last several generations. Such is the potential social upheaval that tech pioneer Bill Gates has proposed taxing robots to slow their deployment, in a clear signal he believes that less, and slower, progress is necessary to mitigate the social risks. Â
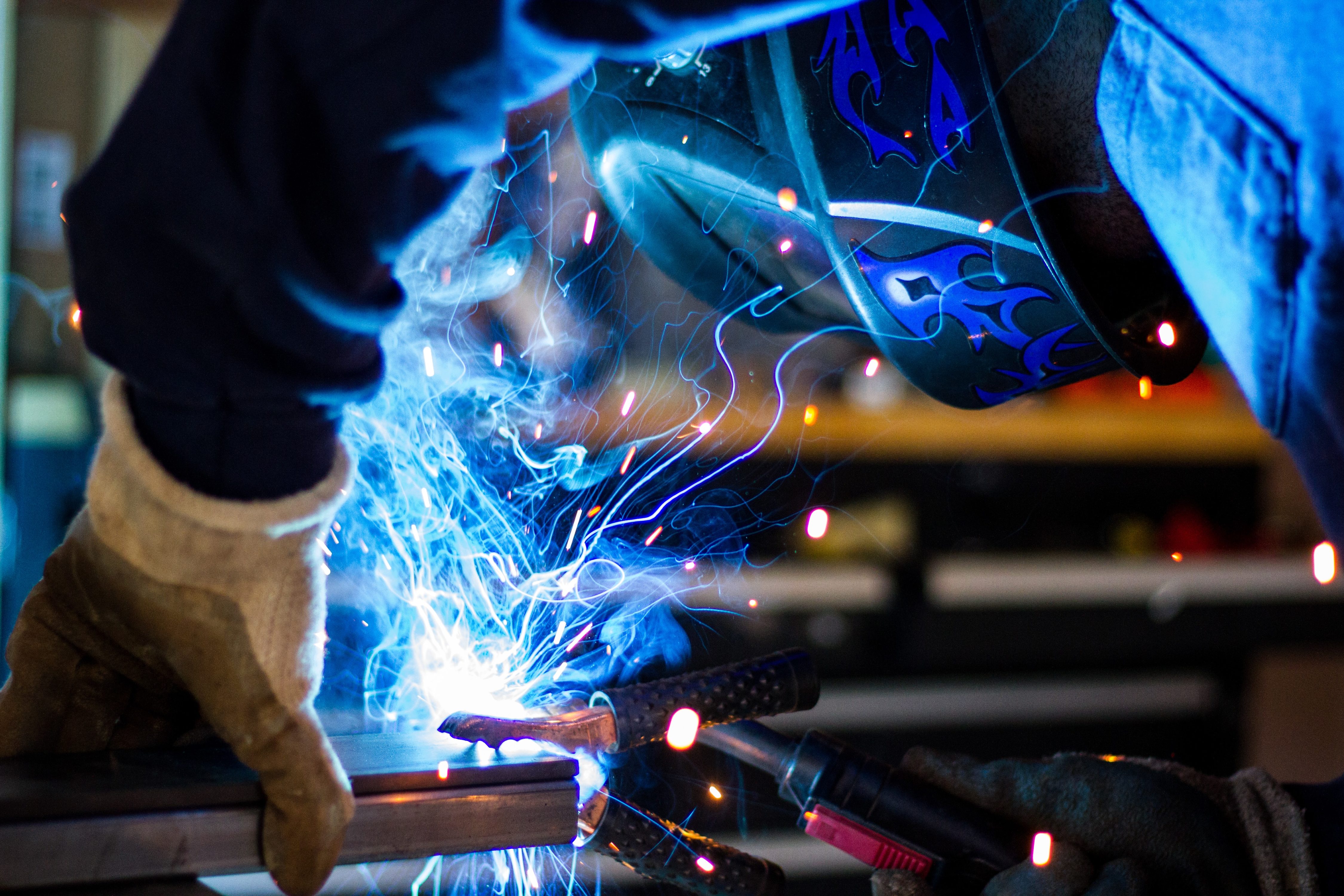
The result of having so many goods and services provided by non-human hands may be a world which has the ability to generate enough wealth for everyone, but which is not efficiently distributed, driving up inequality. Some technologists like Elon Musk have imagined the adoption of new social models like universal basic income to distribute the gains. Author and trade and international economics editor at The Economist Ryan Avent, to explore another dimension of the question, points to the social benefit of gainful employment as a cohesive force that brings meaning and a sense of accomplishment, dignity, and self-worth to peopleâs lives, and solutions like universal basic income donât address this issues.Â
It needs to be pointed out that all predictions of robot overlords have not yet come to pass. In 2014, Morgan Stanley predicted fully autonomous vehicles capability in 2022, yet we are not even close. With US unemployment at a 50-year low, any arguments that the introduction of I4.0 will lead to mass unemployment are understandably difficult to embrace at the moment.Â
Current events are leading to another lens through which to view the employment impacts of I4.0. The myriad supply chain snarls seen since 2020 have seen companies rethink their global supply chain footprints. A key result of the rethink is growing re/near/onshoring. Robotics and automation are making this decision easier for companies by partly mitigating the increased labor costs that will come with increased domestic employment.Â
WasteÂ
As I4.0 becomes more widely deployed, there are many reasons one should expect companies to have less inventory overall, and correspondingly less waste needing disposal, as I4.0 capabilities address each of the drivers that lead to increased inventory in the chain.Â
One of the principal reasons companies carry surplus inventory is due to production batch sizes. Larger batch sizes lead to clear, quantifiable cost of goods savings, but also to larger overall inventory levels. As capabilities like 3D printing and line changeover automation improve, batch sizes for many products or components may be one unit, ideal for slow-moving items.Â
There are other, more subtle, inventory benefits. The automation that is enabling companies to bring production back to developed markets also comes with the benefit that there is less inventory caught up in international freight. On top of that, the faster lead times that come with domestic production also mean less safety stock needed to protect against unforeseen demand. Continuing this line of thinking, artificial intelligence and machine learning are demonstrating superior ability to predict consumer demand, leading to ever smaller safety stocks.Â
SafetyÂ
One more subtle impact of I4.0 technologies is on the question of workplace safety. Factories can be dangerous places, and worker safety is always a paramount concern. But the less workers there are in factories, the fewer industrial accidents will occur. Having dark, fully automated manufacturing implies safer worker conditions â though this also implies fewer workers.Â
Without going that far in the reflection, technologies like automated guided vehicles (AGVs), used to manage intralogistics like forklift activities, are perhaps safer than human drivers in the scope of the tasks they are suited for. This is true not only for incidents involving moving vehicles but also for workplace hygiene. Pallets are always placed in the exact foreseen spot, meaning fewer trip hazards.Â
Product valueÂ
I4.0 is bringing improvement to the value proposition companies offer to their customers, both in product and service. Â
The most prominent one is the advent of e-commerce. Growing slowly over time, e-commerce took a step forward during the pandemic, where the ability to order almost anything and have it delivered to oneâs door became a vital part of coping and getting through the crisis. Without the myriad of I4.0 tools like cloud computing, order management systems, chatbots and the like, many companies would not have been able to scale up their e-commerce capabilities so quickly or at an acceptable cost. Amazon has now surpassed Wal-Mart as the largest retailer outside of China. Itâs fair to say that this convenience is here to stay and will only grow.Â
Behind the scenes, AI-powered planning tools are improving the ability of companies to predict consumer demand and deploy inventory efficiently so the consumer sees fewer empty shelves. This can be hard to believe after more than two years of retail shortages, but it would have been much worse if the pandemic has struck 10 years earlier.Â
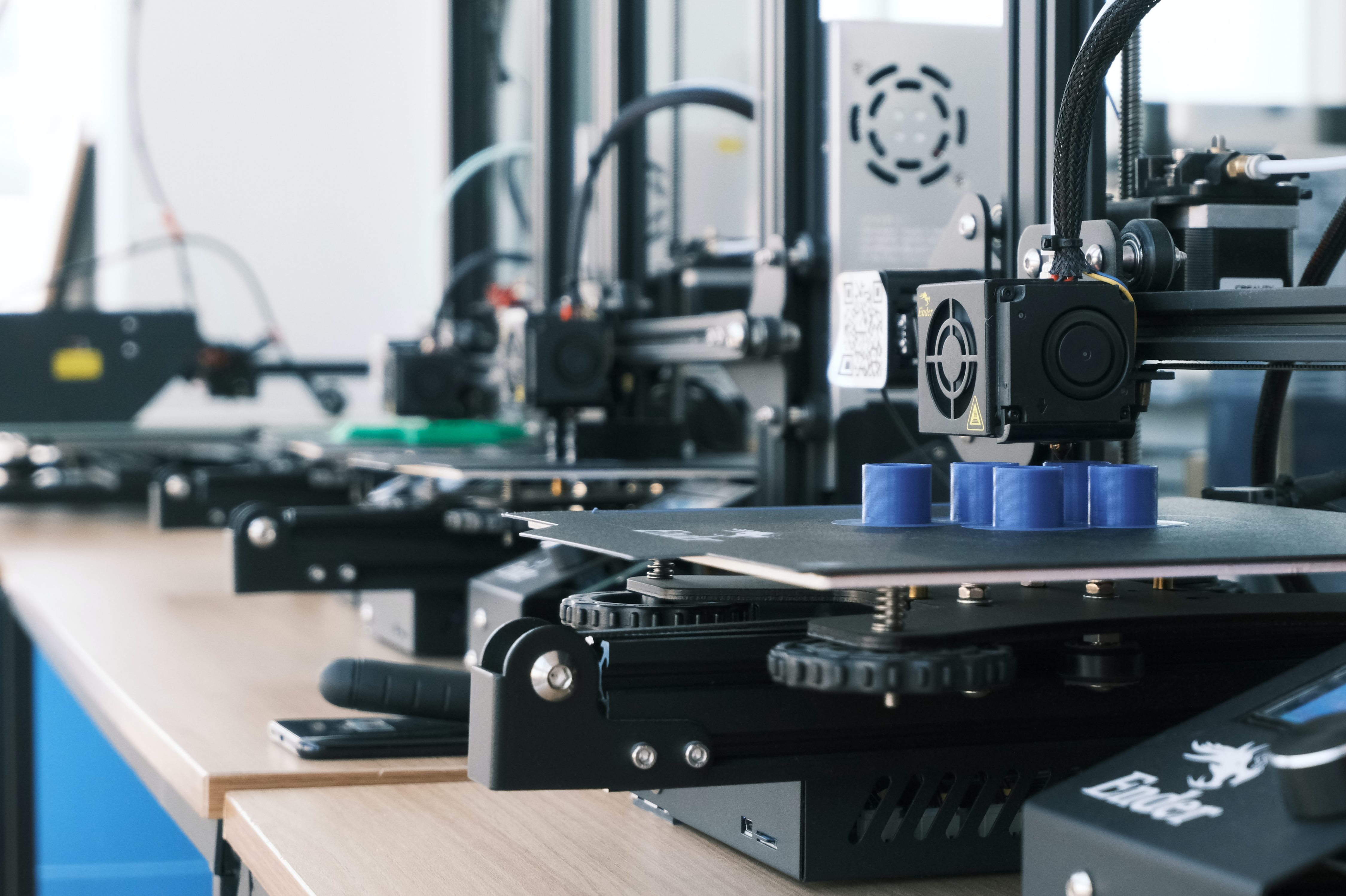
The consumer delight does not end there. The products themselves are changing technologies like 3D printing and micro-factories are powering growing product personalization, allowing consumers to more choice in form and function without paying more.Â
There is even an argument to be made that product quality is increasing as well. Computer vision and AI has enabled companies to identify quality issues in products before they are packed and shipped. With the use of advanced analytics, the root causes of quality problems can be found and addressed by identifying patterns impossible for humans to discern. In the event there is a quality issue, tools like RFID and product serialization make recalls faster and more efficient. Overall, McKinsey predicts a reduction of up to 20% in the cost of non-quality thanks to I4.0.Â
ClimateÂ
Many of the impacts discussed here also have a climate dimension to them, in addition to other consequences.Â
Bringing manufacturing closer to the largest markets in developed countries means having much less distance for the goods to cover from factory floor to end user. The continued electrification of ground fleets means that not only are trips shorter, but there are greener options for freight. Also, higher proximity means less air freight for expedited shipment in addition to less ocean freight.Â
One of the implications of greater automation in factories is that, should production become fully automated, the energy footprint from lighting and heating can be lowered, resulting in so-called âdark factoriesâ.Â
Some I4.0 technology directly targets energy usage, where the climate footprint is a direct consequence. Leveraging Internet of Things and AI/ML much in the same way as predictive maintenance, smart energy applications look for ways to lower lighting and heating at times and locations where it is less needed.Â
There are downsides to consider as well. Many I4.0 technologies rely on cloud computing, which in turn relies on energy-greedy data centers. Current estimates project that by 2025 data centers will account for more than 3% of global carbon emissions, and already today the carbon footprint of data centers are the same as the entire aviation industry. Of course, not all data center activity is I4.0, but many I4.0 technologies rely on processing huge amounts of data over the internet.Â
Taking a step backÂ
Through the many lenses seen here, particularly that of social impacts, there are trade-offs to be considered as I4.0 continues to gain traction and deploy more widely. This has been true for every major step in the direction of progress in the past, just as it is now.Â
Whether one deems the Fourth Industrial Revolution to be âTech for Goodâ or tech for bad depends both on how far the operations world takes the deployment and where oneâs personal priorities lie. What is certain is that the question is a valid one to ask, to debate, and to challenge ourselves with as innovation continues apace. If Industry 4.0 is truly a revolution, we must be mindful of all possible implications â both positive and negative.Â
For further reading on the latest industry trends in the global supply chain agenda, please read⯠this article, based on the third edition of the IMD Global Supply Chain Survey.