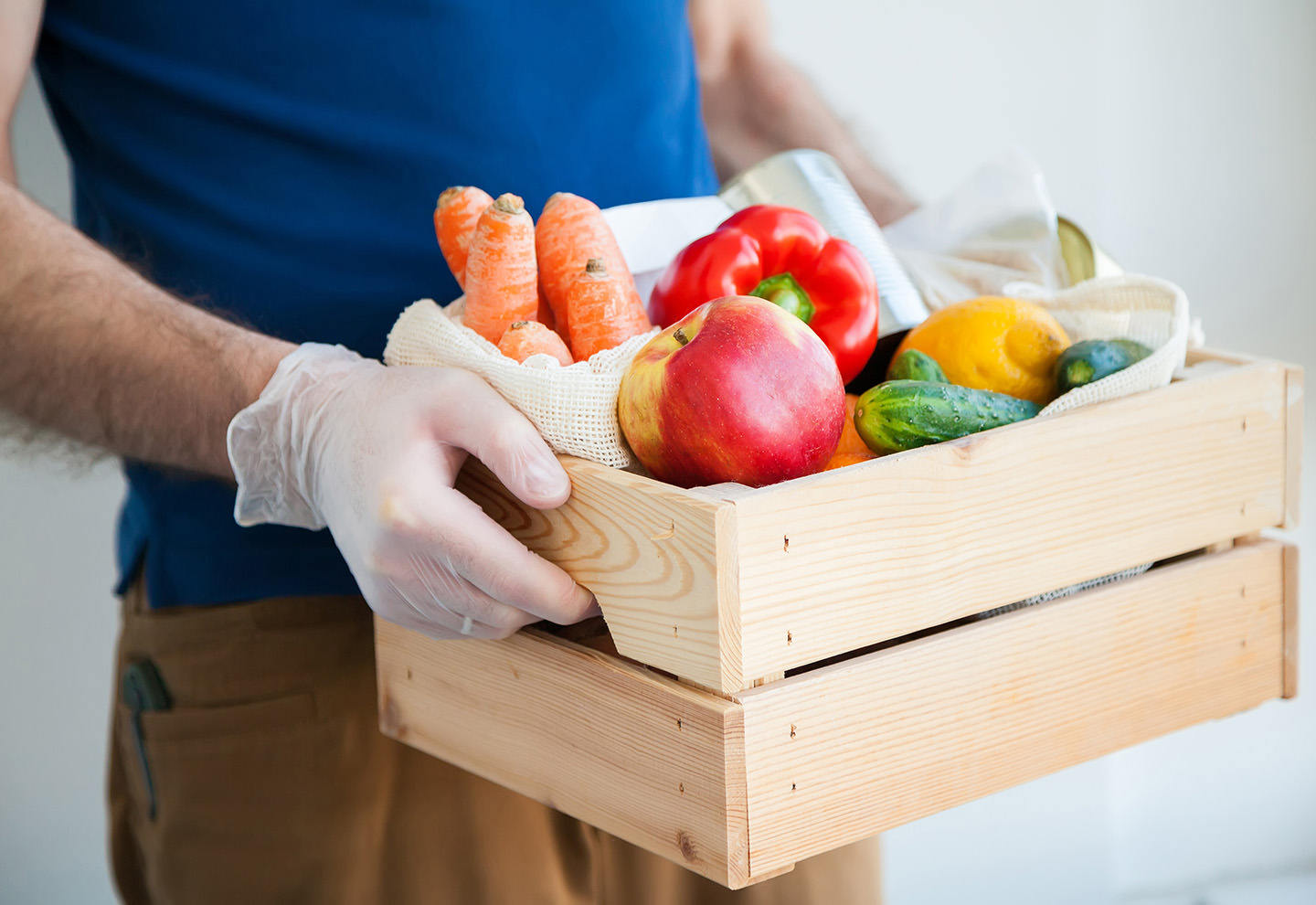
A post COVID-19 outlook: the future of the supply chain
As the Coronavirus wreaks economic turmoil around the world, modern supply chains face unprecedented stress and are drawing an increased level of scrutiny.
For months prior to the COVID-19 crisis, trade tensions had been mounting due to the escalating tariff war between Washington and Beijing, and a broader populist streak running through several other capital cities. This rise in protectionism, coupled with concrete costs and new financial barriers, fueled broader challenges and concerns for logistics networks operating on the global level.
Today’s globalized supply chain network has been optimized to identify minimum lead times at the lowest possible price. We want electronics made in China, so we can buy them cheap.
However, rapid political developments, a shift towards consumers buying niche products and, now, global pandemics have revealed the weakness that lies at the heart of this model of manufacturing.
The hidden costs of single-source dependencies and poor flexibility in adapting to real-time shocks have been laid bare. Today, we will tolerate higher prices for certain goods, if it means we get them faster and more in line with our aspirations.
As a result, the change that had already begun, towards more flexibility and multi-level sourcing, will accelerate tremendously. Over the next years, we can expect to see a broad overhaul of our supply chain infrastructure and a new order based on three key dimensions:
From globalization to regionalization
Logistics hubs will re-emerge at the regional level. To eliminate single-source dependencies, and to establish a flexible and adaptable supply chain, product integrators, sub-system suppliers and component suppliers will source, assemble and deliver from their own backyards.
That change had been kicked off several years ago because of increasing Chinese labor costs. Once the major attraction for companies towards Asia, the labor cost differential has shrunk over the past few years. What continues to hold foreign attention, however, is the whole supply chain network of suppliers and sub-suppliers located in those Chinese hubs.
Today, large electronic equipment manufacturers source about 40% of their parts from China including sub assembly. Given the incredibly high number of parts required – each with different lead times – a return to regional supply chains presents an incredibly complex challenge. However, that challenge might be worth taking in the post-COVID world.
We have seen the impact of global sourcing in the pharmaceutical industry in Europe, which has imported 80% of the active components for its drug supply from China and India. In the post-COVID future, it’s entirely expected, that European governments would ensure they could draw these supplies from their own region. Thus, we could soon see a purposeful shift to regional sourcing.
The supply chain: The new protagonist and the stress test
Since the 2008 financial meltdown, regulated financial institutions globally have been forced to stress test their balance sheets to assure preparedness for an economic shock. Governments wouldn’t have it any other way.
Similarly, a series of large-scale cyber-attacks in the past 10 years has forced technology companies to institute penetration tests to scrutinize their cyber-security mechanisms. Boards of directors won’t have it any other way.
In a post-COVID-19 world, supply chain stress tests will become a new norm. The distributed global business model, optimized for minimum cost, is finished. Tomorrow’s model demands new priorities in optimization.
The supply chain has become a main protagonist everywhere, it has moved from playing a “behind the scenes” organizational role to being a prime driver of the company business.
In the past, volume stability enabled the supply chain to deliver with a high level of service while lowering costs at the accepted quality. However, supply chains and manufacturing plants allow minimal flexibility in terms of volume – as the struggle to fulfill ventilator demand has exposed.
As volumes become more variable, supply chains must become more adaptive, especially if, as forecasts suggest, large suppliers and logistics operators in the supply chain industry must prepare for major catastrophic events such as weather events (fires, flood, tsunami), lethal pandemic outbreaks, strikes, social unrest and associated disruptions.
To maneuver choppy waters, navigators need visibility. In certain industries, such as microprocessor development or consumer technologies, advanced electronics manufacturers have already produced comprehensive dashboards that lay out the full status of production and shipment, down to the last detail. The dashboards refresh every 20 minutes to provide a real-time overview of the entire supply chain.
Such technology will inevitably emerge as the norm. Consider the pharmaceutical industry, for example, where there is currently no single database, either centralized or distributed, from which to map the critical components for drug manufacturing. For suppliers, and ultimately, end-users, the visibility on sourcing is critical and must be upgraded.
The human dimension is back: Manual steering and volume flexibility
The human dimension is back, and it will play a prime role in rebalancing the global supply chain during this crisis, and well beyond.
Big and unexpected changes in volume render statistical models useless. These assess events such as the pandemic as “outliers” and, therefore, discard them from the data. Although we need visibility for the people in the supply chain to be able to make decisions, most decisions should be made manually. Ergo, the human factor is key.
The Toyota Principle of “autonomation” (automation with a human touch) has been proved to be the most adaptable. This involves automating around 80-90% of the system but allowing a 10-20% opportunity for human expertise to improve system operation. Humans again.
And as unemployment rates rise across the world, healthcare and agriculture industries, as well as grocery stores, and other key “essential work” fields face labor shortages. Amazon announced 100,000 new roles in fulfillment centers and delivery networks, while, in China, the return of quarantined workers to production plants and factories generated relief in the West. Similarly, despite AI’s positive affect on efficient e-commerce, ‘the last mile’ of delivery – from distribution center to doorstep still needs a human driver or drone operator.
Labor should be managed as a key asset of adaptation that plays a fundamental part of a crisis response program. The shortage of N95 masks, for example, requires new manufacturing plants to meet demand, and given the dramatic price increases of up to 5x markups in online retail outlets, increases in labor costs is both feasible and manageable. The opening of a new production line or the modification of an existing one requires a surge in human capital.
COVID-19 has revealed the weaknesses of a globalized manufacturing system and in order to respond we need to fundamentally rethink supply chains. Our goals in the medium term should be making them more regional, modifying the supply chain as a key business driver and putting back the human asset as the most important factor for an agile business to succeed.
Research Information & Knowledge Hub for additional information on IMD publications
The supply chain risk management literature differentiates between disruption risk that arises from supply disruptions to normal activities and recurrent risk that arises from problems in coordinating supply and demand in the absence of disruption...
The US deal granting it future revenue and access to Ukraine’s mineral sector raises a broader question: is this the beginning of a model for American foreign policy, one that links strategic resource access to long-term diplomatic and financial c...
Digital transformation introduces a new set of parameters for firm innovation. Existing literature has found that family firms vary on their willingness to innovate. However, explanations of the factors that lead to a family firm’s (un)willingness...
Multinational businesses are recalibrating their global supply chains, with one eye focused firmly on Washington. As the Donald Trump administration reignites the use of tariffs as a blunt instrument of economic leverage, so-called “friendshoring”...
Research Information & Knowledge Hub for additional information on IMD publications
Research Information & Knowledge Hub for additional information on IMD publications
Research Information & Knowledge Hub for additional information on IMD publications
Research Information & Knowledge Hub for additional information on IMD publications
in Production and Operations Management June 2025, vol. 34, issue 6, https://doi.org/10.1177/10591478241302735
Research Information & Knowledge Hub for additional information on IMD publications
Research Information & Knowledge Hub for additional information on IMD publications
in I by IMD
Research Information & Knowledge Hub for additional information on IMD publications
in Small Business Economics 24 May 2025, ePub before print, https://doi.org/10.1007/s11187-025-01057-8
Research Information & Knowledge Hub for additional information on IMD publications
Research Information & Knowledge Hub for additional information on IMD publications
Research Information & Knowledge Hub for additional information on IMD publications